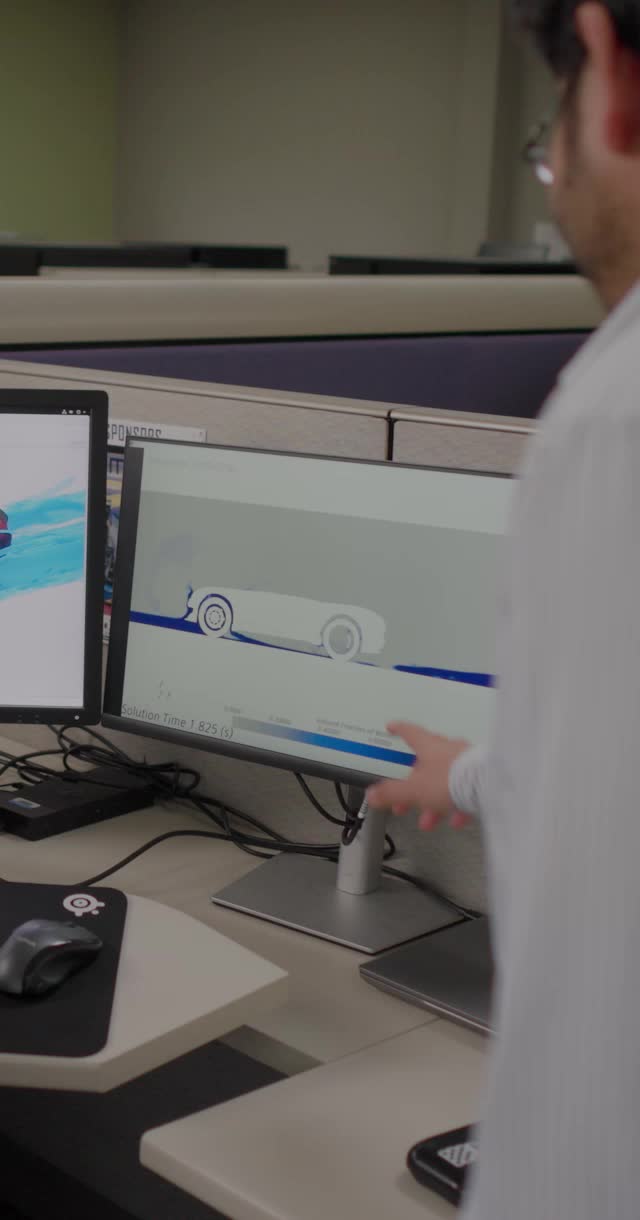
Let’s engineer.
We are in the business of enabling. Transforming. Engineering. Our capabilities are tailored for any customer to unleash a tangible impact in their industry. From consulting, to chassis and body engineering, to EV control systems and powertrain development, it begins with a team of experienced engineers.
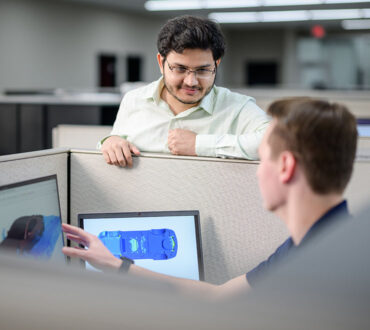
Engineering Services
Need a full suite of engineering services? You’ll find it at Roush. Engineering analysis and consulting, industrial design, and testing and validation are only the start. We also have specialists devoted to specific project requirements, like NVH testing for noise and vibration engineering and functional safety.
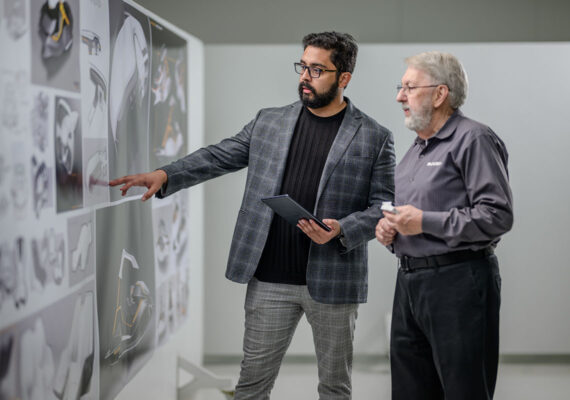
Advanced Engineering
Let’s reach the next level. The Advanced Engineering team at Roush pushes the boundaries of technology to develop solutions that span from concept maturation and optimization to hardware integration and advanced composites development.
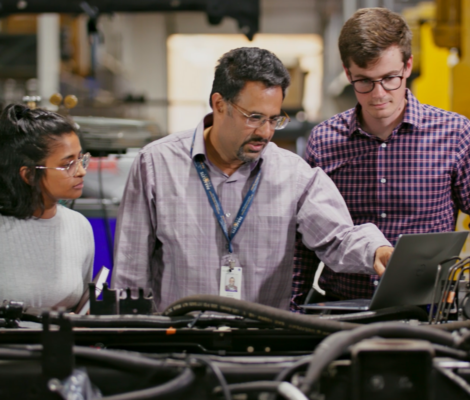
Body, Chassis, and Powertrain Engineering
We support all aspects of vehicle production. Our Body Engineering and Vehicle Integration Group and Chassis Engineering and Vehicle Dynamics team are exclusively assigned to the design and development of intricate vehicle structures.
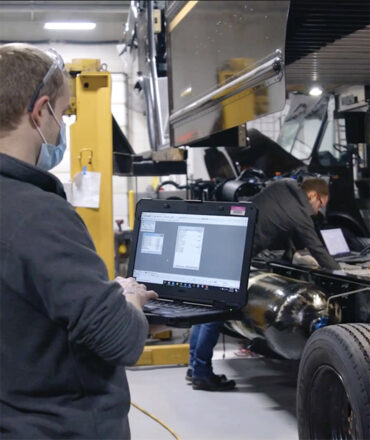
Safety Engineering
A successful project is a safe project. Our dedicated team of core engineers is focused on maximizing functionality in a way that meets — and exceeds — customer safety objectives.
Let’s work together.
Connect With Us